Imagine a workspace where everything is in its designated spot, tools are easily accessible, and the environment is always clean and organized.
This is the promise of 5S Visual Management—a transformative system rooted in the principles of Sort, Set in Order, Shine, Standardize, and Sustain.
We’ve developed a quick guide to help you understand 5s visual management including its steps, its tools, and tips for effective use of it. Keep reading to learn what 5s visual management is and how it can benefit your business.
What is 5s Visual Management?
It is a system that uses visuals to help employees organize and clean their work areas. It’s based on the 5s principles of workplace organization: Sort, Set in Order, Shine, Standardize, and Sustain.
Visual management boards use pictures and symbols to show employees what needs to be done and how it should be done. That makes it easier for employees to understand what they need to do and helps them stay on track.
The Steps Involved in 5s Visual Management
They are also called Principles of 5S Syestem
- Sort (S1) – The first step is to sort through all the items in your work area and eliminate anything unnecessary. That will help reduce clutter and make it easier to find what you need.
- Set in Order (S2) – Once you’ve sorted through your work area, you must put everything in order. That means creating a system for how things will be stored and organized. It will make it easier to find items when needed and help keep your work area tidy.
- Shine (S3) – The next step is to clean your work area. That includes dusting, sweeping, and ensuring that all surfaces are clean. A clean work area is more pleasant to work in and can also help reduce the spread of germs.
- Standardize (S4) – The fourth step is to create standards for your work area. That means setting rules for how things should be done and ensuring everyone follows them. That will help to keep your work area organized and running smoothly.
- Sustain (S5) – The final step is to sustain your work area. That means keeping up with sorting, organizing, and cleaning regularly. Again, making 5s visual management a part of your daily routine is essential so that it becomes second nature.
History of 5s Visual Management
It can be traced back to the early days of the Toyota Production System. Then, Toyota recognized the importance of visuals to help employees organize and clean their work areas. Since then, 5s visual management has become a popular way to improve workplace organization and efficiency.
Tips for Effective Use of 5s Visual Management
Visual management is an essential part of the 5s methodology. It can be used to track progress and ensure that all employees are aware of the goals and objectives of the 5s program. Some tips for using visual management effectively include:
- Use clear and concise visuals to communicate the goals of the 5s program.
- Display the visuals in a prominent location where all employees can see them.
- Update the visuals regularly to reflect the current status of the 5s program.
- Use different types of visuals to appeal to different learning styles. For example, use pictures and text to communicate the goals of the 5s program.
- Keep the visuals simple and easy to understand.
By following these tips, you can ensure that your 5s visual management program is effective and helps improve your workplace’s overall efficiency.
The Different Types of 5s Visual Management Tools
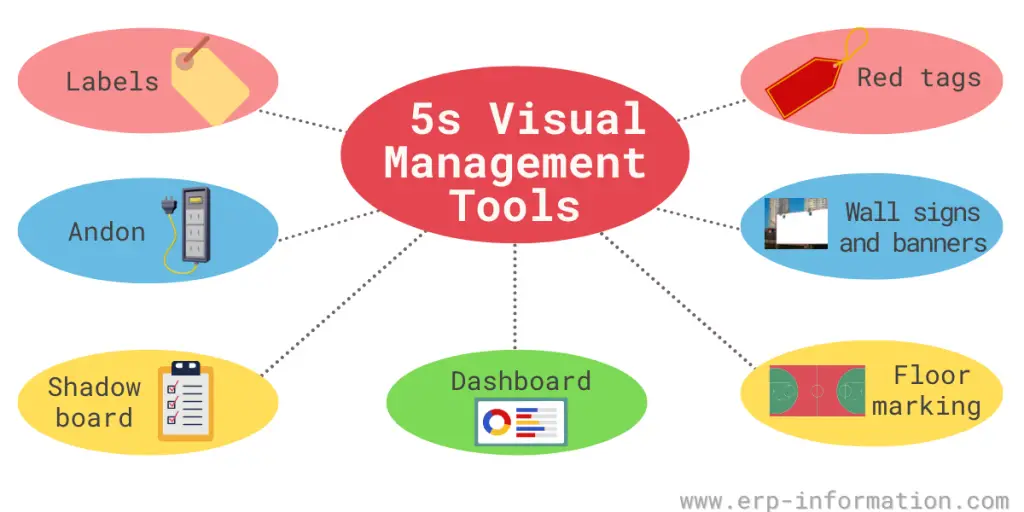
Labels
It is used to identify the content of containers.
Andon
A visual management system used in manufacturing provides real-time information about the production process. It can include Andon boards and andon lights.
Shadow board
A tool used to visually display the presence and missing tools and equipment.
Dashboard
It visually displays the progress of a project or production process.
Floor marking
It marks the floor with visual cues to help employees find their way around the workplace. It also indicates the location of raw materials, finished goods, and shipping.
Wall signs and banners
These tools are used to communicate the goals of the 5s program.
Red tags
Red tags identify materials that should be removed from the workplace.
By using these tools, you can improve the organization and efficiency of your workplace.
Benefits
- Improves workplace organization and efficiency
- Reduces waste and defects
- Improves communication and collaboration
- Increases safety and hygiene
- Improves morale and motivation
- Reduces stress and anxiety
How to Present Visual Management to Your Team?
Following are some tips to present visual management to your team.
1. Encourage Employees to Identify Problem Areas
Start by inviting your team to observe and pinpoint areas in the workspace that are disorganized or inefficient. This collaborative approach helps everyone become more aware of issues and fosters a sense of ownership in the improvement process.
2. Set Criteria for 5S Management
Establish clear criteria for each of the 5S principles—Sort, Set in Order, Shine, Standardize, and Sustain. These criteria will serve as benchmarks for evaluating and improving the workspace, ensuring everyone understands the goals and expectations.
3. Assign Responsibilities to Employees
Delegate specific 5S tasks to individual team members based on their roles and strengths. This not only ensures accountability but also empowers employees to take initiative in maintaining a well-organized and efficient work environment.
4. Collaborate on Improving Efficiency
Engage the team in discussions about how to streamline workflows and eliminate bottlenecks. Collective brainstorming sessions can lead to innovative solutions that enhance productivity and reduce waste.
5. Work Together on Cleanliness
Organize team activities focused on cleaning and tidying the workspace. Regular group cleaning efforts can boost morale and ensure that cleanliness standards are consistently met.
6. Develop a Plan with Your Team
Create a comprehensive 5S implementation plan together, outlining the steps, timelines, and resources needed. Involving the team in planning ensures that everyone is committed to the process and understands their role in its success.
7. Design a Chart and Allocate Tasks Equally
Develop a visual chart that outlines all 5S tasks and assign them evenly among team members. This chart should be prominently displayed to track progress and ensure that responsibilities are clearly communicated and shared.
8. Promote Regular Individual and Company Audits
Encourage team members to conduct regular self-assessments and schedule periodic company-wide audits. These evaluations help maintain high standards, identify areas for improvement, and reinforce the importance of ongoing commitment to the 5S principles.
FAQs
Why is 5s visual management important?
Visual management is an important part of the 5s methodology. It can be used to track progress and ensure that all employees are aware of the goals and objectives of the 5s program.
What are some of the challenges associated with 5s visual management?
Some challenges associated with 5s visual management include maintaining the visuals, ensuring that all employees understand the system, and updating the visuals promptly.
How can 5s visual management help improve productivity and efficiency?
This management can help improve productivity and efficiency by providing a visual way to track progress and identify issues.
A visual display of the work area makes it easier to see when something is out of place or work is behind schedule. That can help quickly identify and fix problems, preventing them from becoming more significant issues.
Conclusion
Visual management is essential for any business looking to improve efficiency and reduce waste. The 5s methodology is a great place to start when implementing visual management in your workplace.
By using transparent displays and organizing tools, you can help employees understand their roles and responsibilities more clearly. Visual management can also help you track progress and identify areas of improvement.
We hope this article has given you a better understanding of 5s visual management and how it can benefit your business. Thanks for reading!