3D printing has revolutionized the manufacturing industry, still creating objects can still be slow and difficult.
Additive manufacturing is the future of 3D printing. You can create complex shapes and designs quickly and easily. Subtractive manufacturing is one more type of manufacturing method.
This blog post is about additive manufacturing, which covers working, types, data sets, technologies and applications of AM, and more.
Evaluate 3D print time using our online 3D Print Time Calculator
What is Additive Manufacturing?
Additive Manufacturing (AM) is the process of fabricating three-dimensional solid objects from a digital file. It is also known as 3D printing.
The objects are created by successively adding material layer by layer until the desired shape is achieved. Every layer can be observed as a thinly sliced horizontal cross-section of the eventual object.
AM has been around for over three decades, and its applications have been growing steadily.
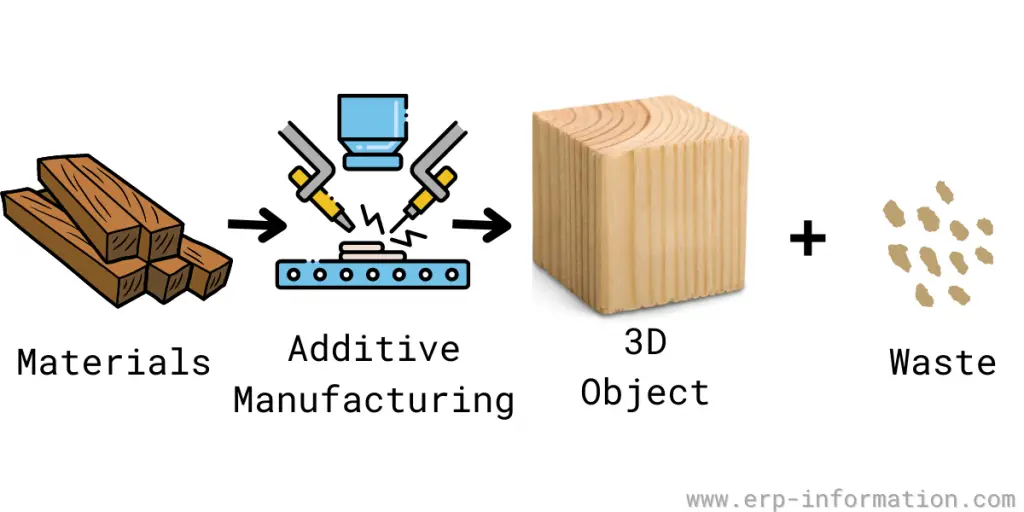
Additive Manufacturing Materials
AM uses a variety of materials to create objects layer by layer. The types of materials used in additive manufacturing depend on the specific process and equipment used, but commonly used materials include:
- Thermoplastics such as acrylonitrile butadiene styrene (ABS), polylactic acid (PLA), and polyethylene terephthalate (PET).
- Metals include aluminum, titanium, copper, and stainless steel.
- Ceramic materials such as glass, porcelain, and piezoceramics.
- Composites such as carbon fiber, fiberglass, and graphene.
- Bio-compatible and resorbable materials include polycaprolactone (PCL), hydroxyapatite, and collagen.
- Sand and powder materials or binders for mold making
The selection of materials, machinery, and processes depends on the application or the final use of the product to be manufactured.
How Does Additive Manufacturing Work?
AM consists of mainly three steps. they are,
3D CAD model
The manufacturing process usually starts with a 3D CAD model of the object that is to be printed. This file is sliced into skinny layers, and the software determines the path each layer should take to build the object.
Deposition
Next, a printing bed is leveled and calibrated using a grid pattern. The printer then prints a very thin layer of adhesive onto the bed.
The print head deposits tiny drops of molten polymer material on these adhesive dots. The drops are deposited so that they fuse to form a single solid layer.
Layering
The print head then moves down by one layer of thickness and repeats the process. That continues until the entire object has been built up one layer at a time.
Support structures are often used to build complex objects. These structures can be made of the same material as the object or from a dissolvable material.
Types of Additive Manufacturing Process
Binder Jetting
A binding agent is used in binder jetting to adhere the metal powder together. The binder can be applied in multiple ways, such as ink-jetting, aerosol, or spray.
Once the binder is used, the powder is selectively deposited in the build area layer by layer. The build area is then cured, and the excess layer of powder is removed. The binder is then removed, leaving behind the metal object.
Directed Energy Deposition
Directed energy deposition (DED) is a process where an energy source is used to melt the metal powder as it is deposited into the building area.
The energy source can be a laser, an electron beam, or a plasma torch. The metal powder is melted and solidified as it cools, creating the object layer by layer.
Material Extrusion
In material extrusion, a filament of plastic or metal is fed through a nozzle that melts the material. The melted material is then deposited on the build area layer by layer. The object is built up from the bottom up.
Powder Bed Fusion
In powder bed fusion (PBF), a layer of metal powder is deposited on the build area. The build area is then heated until the metal powder melts and fuses. The object is built up from the bottom up.
Sheet Lamination
In sheet lamination, thin metal sheets are bonded together using adhesive or welding. The sheets are then cut to shape and layered on top of each other to create the object.
Vat Photopolymerization
In vat photopolymerization, a photopolymer is used to create the object. The photopolymer is a liquid that solidifies when exposed to light. The photopolymer is deposited in the building area and then exposed to sunlight. The thing is built up from the bottom up.
Dataset
Several critical datasets are associated, including,
- Build data includes information on the geometry of the part being built and the build parameters used.
- Material data provides information on the properties of the materials being used in the build process.
- Process data includes information on the build process, such as build time, layer thickness, Etc.
Technologies Used in Additive Manufacturing
Here are some of the most popular AM technologies being used today:
Stereolithography (SLA)
Stereolithography is one of the oldest and most popular additive manufacturing technologies. It works by curing liquid resin with a laser to create successive layers of a 3D model.
SLA is known for its accuracy and fine details, making it ideal for prototypes and complex engineering models.
Fused Deposition Modeling (FDM)
Fused deposition modeling is a widely used technology that extrudes heated thermoplastic filament layer-by-layer to build 3D objects. FDM is known for its affordability and ease of use, making it a popular choice for home and hobbyists.
Selective Laser Sintering (SLS)
SLS technology uses a laser to fuse small plastic, metal, or ceramic powder particles.
Metal Additive Manufacturing (MAM)
Metal additive manufacturing creates metal parts from powder using an energy source to fuse the powder.
Direct Metal Laser Sintering (DMLS)
Direct metal laser sintering is a type of MAM that uses a laser to fuse small particles of metal powder.
Industries that use Additive Manufacturing
Aerospace
Aerospace is one of the early adopters of AM technology. For example, aerospace companies use additive manufacturing to produce aircraft engine brackets, pilot seats, and landing gear components.
Automotive
The automotive industry is another primary adopter of additive manufacturing technology. Automotive companies use it to produce prototypes and end-use parts such as air vents, fuel tanks, and brake components.
Healthcare
The medical industry is a significant adopter of additive manufacturing technology. For example, manufacturing patient-specific tubular continuum manipulators allow for minimally invasive surgery. In addition, dental labs use 3D printing to create dental crowns, bridges, and dentures.
Consumer products
Additive manufacturing is used extensively in the consumer goods industry for prototyping, tooling, and low-volume production.
For example, consumer goods companies use 3D printing to produce eyeglasses, hearing aids, and other wearable devices.
Challenges Associated with Additive Manufacturing
The three main challenges associated with AM are quality control, cost, and speed.
1. Quality control
Additive manufacturing is a relatively new technology, and quality control standards are still being developed.
Many factors can affect the quality of an additively manufactured part, such as material properties, build parameters, post-processing, Etc.
2. Cost
One of the biggest challenges associated with additive manufacturing is the high cost of 3D printers and materials. The cost of additively manufactured parts often depends on the domain’s size and complexity.
3. Speed
Additive manufacturing is typically slower than traditional manufacturing methods. The speed of it often depends on the part’s size and complexity.
Additionally, there are often issues with accuracy and repeatability, and it can be not easy to produce large quantities of parts.
Advantages
- Additive manufacturing can create complex geometries with traditional manufacturing methods that would be impossible to complete.
- It can create on-demand parts, reducing lead time and inventory costs.
- It can be used to create parts with lighter weight, less material waste, and better mechanical properties.
- It can create objects from a variety of materials with intricate details.
- It can also be used to create objects with multiple colors and can be used to create objects with embedded electronics.
Additive Manufacturing vs Conventional Manufacturing
Additive Manufacturing | Conventional Manufacturing |
The most obvious is that it builds objects by adding material layer by layer. | It generally involves removing material to create the desired shape. |
It can create highly customized products or objects. | It is often more limited in the customization of objects. |
The types of equipment can be programmed to create almost any three-dimensional shape imaginable. | It generally relies on pre-existing molds or templates. |
Additive manufacturing processes are typically much faster than their traditional counterparts. | It is slow as its equipment requires more set-up time. |
FAQs
Which materials are used in Additive Manufacturing?
There are a variety of materials that can be used in additive manufacturing, including
1. Metals
2. Plastics
3. Composites
These materials have pros and cons depending on the application.
For example, metals are strong and durable but can be pretty heavy, while plastics are lightweight but may not be as strong or long-lasting. Composites can offer the best of both worlds in terms of strength and weight but can be more expensive than other materials.
What is Ultrasonic Additive Manufacturing?
UMA is an additive manufacturing method that uses ultrasonic welding to join layers of metal foil together to create complex 3D shapes.
It is a solid-state welding process in which layers of metal foils are bonded together using high-frequency ultrasonic vibrations rather than traditional heat-based methods.
It has the advantage that it can manufacture dissimilar metals and allows small, complex structures to be created with complex geometries.
As a result, UAM has several applications in the aerospace, automotive, and medical industries, where the capacity to create complex shapes and structures is critical.
Conclusion
In conclusion, additive manufacturing is a versatile and rapidly growing technology with many advantages over conventional manufacturing techniques.
For example, it can create complex geometries, produce on-demand parts, and reduce lead time and inventory costs.
However, there are several critical differences between additive and conventional manufacturing, including how objects are created and the possible customization level. Nevertheless, additive manufacturing is a versatile technology with a bright future.