The current blog brings to you an innovative manufacturing method developed in the late 20th century by Toyota in Japan to reduce costs, increase productivity, and enhance customer.
Many manufacturers have adopted this global phenomenon to enhance their efficacy. Read further to know about it.
Read the blog post to learn about lean manufacturing’s definition, importance, history, and principles in this post. It also discloses the types of waste.
Definition
Lean manufacturing is a production and inventory control system that emphasizes minimizing waste in every aspect of the business.
It is a process-oriented approach for operations to view each step in the manufacturing journey as an opportunity to increase efficiency and make it cost-effective.
It aims to improve quality, reduce lead times, maximize customer satisfaction, and eliminate wasteful activities.
Importance of lean manufacturing
The goal of lean manufacturing is to maximize productivity while minimizing waste. Whether using idle workers, improving processes, or utilizing resources more effectively, this technique comes with many capabilities, such as: increased profitability and improved customer satisfaction, that would benefit businesses significantly.
It offers four key benefits:
- Eliminating waste
- Improving quality
- Reducing costs
- Reducing time
History of lean manufacturing
Henry Ford pioneered modern manufacturing, creating a production system called mass production. This system delivered well-fitted components that were interchangeable, manufactured, and assembled within minutes rather than hours or days. During World War II, the US military adopted this mass production system.
Eiji Toyoda, a nephew of Sakichi Toyoda who founded the toy company that would become Toyota, visited Ford’s Dearborn plant in 1950 and realized that their mass production system was not feasible in Japan due to its small and diverse market.
Toyota then teamed up with Taiichi Ohno to develop a new means of production called the Toyota Production System. The idea was to right-size machines for the required volume and introduce self-monitoring machines so products could be produced faster, with reduced costs, be varied, and maintain high quality.
The Toyota Production System (TPS) was established on Jidoka and Just-in-Time principles. Jidoka focuses on preventing defective products from being produced by ensuring that when a problem arises, the equipment stops immediately. This allows a single worker to control many machines while quickly identifying and addressing problems.
Just-in-Time follows the principle of making what is required and the exact amount required when it is needed. Through this approach, Toyota eliminates waste while producing high-quality products efficiently. The TPS aims to create products of sound quality, one at a time, that fulfill customer requirements.
The principles of Lean were originally outlined in the book written by James P. Womack, Daniel T. Jones, and Daniel Roos- The Machine That Changed the World, based on their observations at Toyota.
The principles of lean manufacturing
The lean methodology helps streamline production systems through these principles, making it easier to understand, do, and manage work.
We discuss the five key principles of lean manufacturing to boost your manufacturing process.
Identify value
The goal of manufacturers and service providers is value creation while still making a profit by limiting waste and costs. Customers finally decide the value of the products or services based on how much they are willing to pay for them.
Map the value stream
Value stream mapping allows managers to view each step in the production process to locate and reduce waste and identify areas for improvement.
Create flow
Lean manufacturing aims to strengthen processes, and as and when the steps in the value stream are improved, production lead times are usually shortened.
Establish a pull system
The pull system is when work is initiated only when a customer orders allowing for just-in-time productions.
Pursue perfection
The objective of this technique is to strive for perfection, which leads to a continuous decrease in steps and required time.
Lean manufacturing and types of waste
It attempts to bring about continuous improvements to systematize, reduce or simplify the seven main types of inefficiency to maximize results with minimum available resources. Thus, eliminating waste is the main agenda.
The seven types of waste that do not provide any value addition for the customer
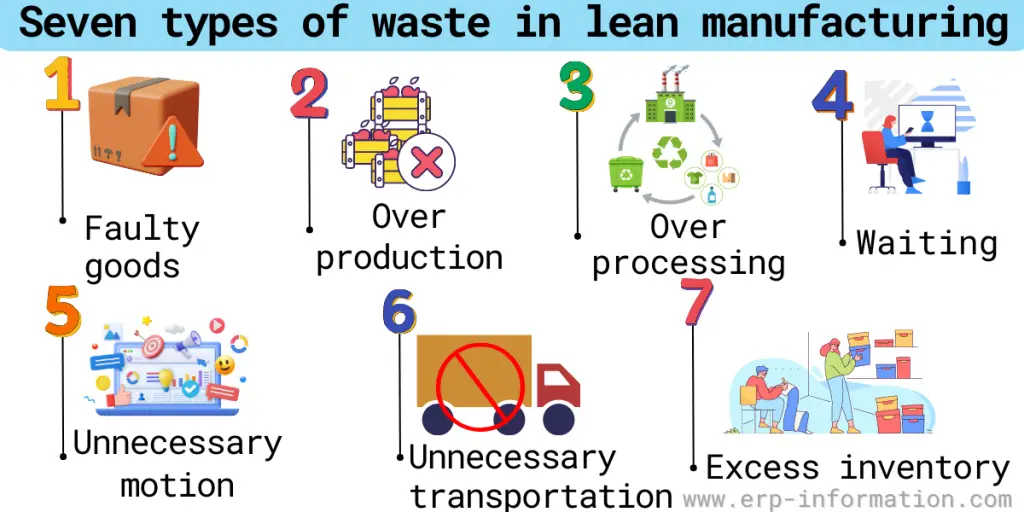
- Faulty goods or Defects: Failing to meet quality standards can lead to many issues, leading to unhappy customers and increased expenses.
- Over-production: Producing more than required wastes resources and time and incurs additional costs.
- Over-processing: Adding unnecessary components or features is a waste since the customer would not benefit greatly from this.
- Waiting: When any service is not active, the workers are waiting for materials, approval, or suppliers, and the equipment needs to be repaired.
- Unnecessary motion: Non-optimized movement of people and equipment.
- Unnecessary transportation: Any unnecessary movement of materials and resources harms overall efficiency.
- Excess inventory: Overstocking resources to meet customer demands is another waste resulting in increased storage costs and no value addition for customers.
It has been recognized as a means to identify and reduce the main wastes of production. In addition, experts have proposed an eighth waste type – unused talent or ingenuity that occurs when workers’ ideas for improving processes need to be recognized.
Simplifying the waste types into three broader categories can help make it easier for your team to understand :
- Mura: Unevenness or waste. It results from fluctuating demand, either from customer requests or an organization’s inclusion of new services.
- Muri: Overburden or waste due to trying to do too much. People can be asked to do too much, resulting in poor resource allocation and waste of time as they switch tasks or lose motivation due to being overburdened.
- Muda: No effective value addition. Activities that don’t add value or support other activities that do should be eliminated to avoid wasting resources.
This is all about making things better and examining the existing processes, and trying to improve them for efficiency; here are four main objectives of Lean manufacturing are :
- Improve the quality of value delivered,
- Cut down on the delivery times and response rates
- Optimize work processes by removing non-essential steps
- Reduce costs while still meeting customer requirements.
Advantages
Understanding the benefits of lean manufacturing to implement it suitably in your organizations:
- Enhanced quality
- Improved employee and customer satisfaction
- Improved productiveness
- Profitability
- Waste reduction
- Streamlined operations
Tools of lean manufacturing
To implement lean principles in a manufacturing setting, you’ll need to use specific tools to identify and eliminate waste; Here are some of the popularly used ones:
- Kanban boards (graphics that represent workflow)
- Control charts (for supervising workloads).
- Poka-yoke (used to avoid errors)
- Total productive maintenance (improves the quality of the process)
- Rank order clustering (for production flow examination)
- SMED (Quick way to transition in between manufacturing processes),
- Value stream mapping (probable improvement opportunities)
- 5S (an organization system for the workspace)
- Single-point scheduling
- Work cell redesign
- Multi-process handling
Implementations of lean manufacturing
Establishing alignment across the organization is key to taking advantage of Lean manufacturing’s advantages, such as more efficiency, agility, and customer responsiveness. Here are the initial steps we advise any organization aiming to roll out Lean manufacturing on a large scale :
- Develop a straightforward manufacturing system
- Constantly strive for improvement
- Continually apply design enhancements.
- Encouraging staff involvement.
As Lean Manufacturing technology has grown over the years, what began as a drive to reduce waste and improve production times in industrial settings is now revolutionizing multiple industries.
Its powerful emphasis on continuous improvement and respect for people leads to unprecedented transformation across domains from traditional manufacturing to healthcare services. Implementations:
- Project management
- Software development
- Construction
- Healthcare
- Banking
- Education
Applications of lean manufacturing
For decades, lean manufacturing methods have helped create tremendous cost and production efficiencies. When used correctly, its implementation brings forth a comprehensive approach to eliminating waste from the entire process chain while delivering tangible value to customers.
Some of the applications:
- Cable manufacturing
- Truck manufacturing
- Automotive industry
- Warehouse management
- Printing Industry
- Customer service
Real-life implementations of lean manufacturing
Gaining insight through investigation of lean methods with some real-world examples.
Toyota
Since implementing the Toyota Production System (TPS), their lean manufacturing model has revolutionized production efficiency.
Its founder, Sakichi Toyoda, was determined to reduce waste at every step by introducing concepts such as jidoka and kaizen, which focused on automated processes that minimized human error while safeguarding product quality standards.
This system achieved unprecedented success when they implemented just-in-time methodologies so only products with existing demand would be manufactured, thus reducing inventory levels and preventing overproduction altogether.
Nike
Nike prioritized building sustainable innovation capabilities with almost 785 contracted overseas factories in their production chain.
By implementing lean manufacturing practices such as continuous improvement and reducing waste, they could ensure product quality and improve working conditions for employees while providing maximum value to customers.
Ford
Ford Motor Company has worked for decades as an industry leader in quality and innovation. To this end, they have implemented various measures such as kaizen methods, Six Sigma processes, Lean Manufacturing techniques, and Total Quality Management (TQM) procedures on their production lines.
Their assembly line system was highly automated and standardized, allowing the company to reduce waste at every stage of the process while still improving product quality – leading to cost savings that benefit everyone.
The efficiency gains made through these strategies were so impressive that even Sakichi Toyoda credited them with inspiring many aspects of Toyota’s Production System.
Bank of America
Bank of America quickly identified where they could be doing better and efficiently implemented lean Six Sigma principles to increase customer satisfaction.
Through its rigorous data-driven methodology, it was able to identify encoding errors, late postings, omissions, and other operational inefficiencies that were leading customers astray.
With targeted metrics for performance assessment set up throughout their organization, the bank is making sure every transaction goes off without a hitch. So you can keep your money transactions hassle-free.
Intel
Intel’s commitment to customer satisfaction is so strong that when demand for its products surged, it didn’t take the easy way out and focused solely on output. Instead, by implementing Lean techniques such as reducing works-in-process (WIP) and ridding waste processes, Intel increased productivity without compromising quality or increasing the risk of product defects.
Effectively balancing efficiency with absolute reliability sets them apart from other semiconductor companies in the industry today.
Conclusion
Many lean manufacturing principles could be adopted and adapted to other businesses, even if you’re not in the manufacturing industry. For example, some of the world’s most successful companies have achieved amazing results by adopting a lean philosophy.
Do you think the article was helpful? We hope this article gives you a better understanding of lean manufacturing and how it can help your organization become more efficient and productive.